Cellulose Nanocrystals
The cellulose sub-elementary fibril in plants is the most abundant nanomaterial on Earth! ~Hiroyuki Yano, Kyoto University

Of the many materials derived from the forest, the one which possesses perhaps the highest strength and stiffness is the cellulose crystal. Industrially, the material which comes closest to crystalline cellulose is known as microcrystalline cellulose (MCC) and has been used since its discovery in the 1960's for a variety of uses, mostly in the pharmaceutical and food industries. Almost every aspirin, or other kind of, tablet contains MCC as the drug carrier or as a processing aid.
MCC (Fig 1) is derived from bleached, dissolving grade wood pulp that has been acid hydrolyzed. Under moderate conditions of acid hydrolysis, the cellulose in the pulp is degraded, but the rate of degree of polymerization (DP) reduction slows after a certain point, fiber degradation takes place.

The cellulose degradation proceeds slowly after this point, which is called the level off degree of polymerization (LODP). Here the cellulose consists of a large size distribution of particles, mostly in the micron range. To produce cellulose nanocrystals (CNCs), the hydrolysis is allowed to proceed further and, under the influence of high shear, the particles are further comminuted. It is possible to produce a reasonable (typically about 30% or so, depending upon species and processing method) yield of nanocrystals of cellulose.
These are the basic crystal units which exist in the crystalline domains of the wood cell wall. Their size varies with species (Table 2), but is on the order of 3-20 nm in width and tens to thousands of nanometers long (Fig. 2). Research interest in cellulose nanocrystals is growing rapidly (see chart). For a brief introduction to nanotechnology and nanocellulose, click here.


Properties of various materials

The Material Science of Cellulose Nanocrystals (PDF)
Cellulose is the largest volume polymer on earth. It is contained in virtually all plants and is produced by certain bacteria and small sea animals. Regardless of its source, cellulose is a semi-crystalline high molecular weight homopolymer of β -1,4 linked anhydroglucose. Being semi-crystalline, cellulose has ordered (crystalline) and disordered (amorphous) regions that allow the generation of stiff nanocrystals. Indeed, acids preferentially hydrolyze the amorphous regions of cellulose yielding dispersions of extremely stiff nanocrystals. The density of CNCs calculated from X-ray diffraction data is 1.566 g/cc and their mechanical performance compares well with other materials (Table 1).

Nanocrystalline cellulose from wood is 3 to 5 nm in width and 20-200 nm long; from Valonia, a sea plant, 20 nm in width and 100-2000 nm long; from cotton, 3-7 nm in width and 100-300 nm long (Fig. 3); from Tunicin, a sea animal, 10 nm in width and 500 – 2000 nm long. Most of these sources provide CNCs with aspect ratios of 50 or greater. This allows for low percolation thresholds.
Acetobacter Xylinum, the most common cellulose producing microorganism, extrudes cellulose I, a two-fold crystalline helix of parallel glucan chains. There are two crystalline modifications to the supramolecular structure of cellulose I: cellulose Iα and Iβ. The crystalline glucan chains are extruded from a terminal complex and aggregate to form nanofibrils, and then ribbons (Fig. 4).
The cellulose crystal is one of the strongest and stiffest organic molecules, with a modulus of 145 GPa and a strength estimated at 7500 MPa. The extension to break of a CNC is estimated to be only 2%. CNCs have high surface areas (~250 m2/g), are hydrophilic, and are quite amenable to surface derivatization. CNCs are long, thin rods with very high aspect ratios (~20-50).

Experiments with CNCs in the Simonsen lab have shown the effect of different interphase chemistries and percolation on nanocomposite performance. We have observed percolation effects at low filler loadings. In addition, we have observed an approximate tripling of both the modulus and water vapor transport in polysulfone at low filler loadings. The choice of CNC fillers therefore provides several distinct advantages:
- They are high aspect ratio nanoparticles, thus the percolation threshold is achieved at low filler loadings
- They have been shown in the literature, and in our labs, to significantly increase the modulus of filled polymer systems.
- Few nanoparticles offer the versatility of CNCs in terms of ease of preparation and chemical modification. Since a major fraction of the polymer matrix will be affected by the CNCs, transport and mechanical properties will be correspondingly affected.
To get up close and personal with CNCs, watch this video created by PhD student Christian Buesch. A CNC aerogel was first coated with aluminum oxide using atomic layer deposition. This prevented electron beam damage to the cellulose. Then the coated aerogel was imaged using the OSU Titan TEM 80-200. The image series obtained was reconstructed and rendered using Avizo software. These images can be used to measure the cross sectional dimensions of CNCs, and to examine the aerogel structure, i.e. how many CNC-CNC contact point are crosses, or X's, how many are T's, and how many are end-to-end connections. Combined with special nanoindentation measurements we hope to be able to evaluate the mechanical properties of the cellulose-cellulose bond.
CNC-Based Polymer Nanocomposites – Recent Experiments
a) Carboxymethyl cellulose (CMC)
CNXLs from cotton were dispersed in CMC (molecular weight 250,000, degree of substitution 1.2) films. Strength, stiffness and toughness were all increased. For example, the tensile strength was increased from 37 MPa to 80 MPa by the addition of 5% CNCs. The films were highly susceptible to water, but a simple heat treatment (120 °C/3 hr) resulted in a water resistant film. FTIR analysis indicated crosslinking between the CMC matrix and the CNC filler. The water vapor transport rate (WVTR) decreased ~ 9% with the heat treatment. This shows the strong improvement in mechanical properties that can be gained with CNC nanoparticles. It also shows that controlling the interphase via the heat treatment did have an effect on the WVTR. The effect is likely not strong here as the CMC itself is quite permeable to water.
b) Poly(vinyl alcohol) (PVOH)
The addition of CNCs to PVOH blends also resulted in improved mechanical properties. In addition, in heat treated films (170 °C/45 min) the WVTR was reduced from ~800 g/m2 day for 100% PVOH to ~ 300 g/m2 day for PVOH with a 10% loading of CNXLs. Again, FTIR indicated crosslinking between the CNCs and the PVOH matrix. This dramatic reduction underscores the potential of the “nano” effect to alter composite properties at low filler loadings.
In the preceding examples, the matrix polymer was hydrophilic, and the effect of constricting the interphase by crosslinking was to reduce the WVTR. PSf showed the opposite effect (Fig. 5). Here the filler is more hydrophilic than the matrix and the WVTR increases with filler content. Also, the percolation threshold at ~ 1% filler loading is clearly demonstrated. The high variability at the 11% CNC loading is believed to be due to agglomeration, a problem in all nanocomposite systems.
The results suggest that the diffusion of moisture is greatly enhanced in the interphase between the CNC filler and the PSf matrix. In this case, the CNCs were not chemically modified.
This demonstration of opposite effects on membrane performance utilizing the same filler suggests that an understanding of the interphase chemistry and physics and careful balancing of the various forces and processes involved offers the promise of advanced nanocomposites with significantly improved properties.
The effect of the interface, or interphase, in polymer composites, including nanocomposites, is critically important to understanding their properties. Studies of biological systems have shown that optimum properties are not always provided by the strongest and stiffest interphases. For example, bone and muscle are connected via tendons, which are quite flexible at small strains, with an increasing modulus of elasticity as the strain increases. The key here is energy absorption by the interphase. With nanocrystal systems, we should be able to design and build nano-systems with various types of bonding. With proper design, it should be possible to provide for an elastic region where small strains are simply absorbed and the system returns to its original state upon release of the stress. At larger strains and stresses the system might become increasingly stiff, behaving as an elastomer. In fact, various degrees of resistance to movement, or internal friction, can be controlled by careful chemical design of the various components. For example, polymers bonded with covalent cross-links will show different behavior than polymers that are ion-bonded through acid-base groups. A material could be designed in this way to be very robust, tough, resistant to impact, yet quite strong and stiff when extended beyond small strains.
These superior mechanical properties should allow cellulose nanocrystal composites to compete with many engineering plastics. The rich literature on cellulose modification allows for a great variety of products to be designed and manufactured from this technology platform.
While the manufacture of new and robust composite materials is an important objective, perhaps even more important is gaining an understanding of what variables govern their behavior. Development of a knowledge base in this area will help lay the foundation for the evolution of more advanced and specifically designed materials of this type. The development of this knowledge base is our primary objective. In addition, these studies will hopefully add to the understanding of the relationships between interphase strength and stiffness and the final material properties of a composite.
Another reason to choose this system from a materials point of view is that cellulose nanocrystals of a defined size range with modified surfaces could be a desirable model system to explore interactions in composites on the nanoscale and to develop a better understanding of bonding mechanisms in these systems. Such knowledge would have implications not only for the development of CNC-based materials, but also for understanding the interface (interphase) in composites in general, adhesives, and other systems of interest to material scientists.
Thus, by modifying the surface of cellulose nanocrystals appropriately, a variety of bonding types can be explored. Chemical modification of cellulose is a mature technology and many chemical reaction schemes are well-known and well studied. It is possible to synthesize cellulose nanocrystals with a variety of different molecules attached to the surface. The modifications could be designed to create different types of bonding between the nanocrystals. These various nanocrystals could then be processed into a solid material. In this manner, direct control on the molecular level would lead to macroscopically observable material properties.
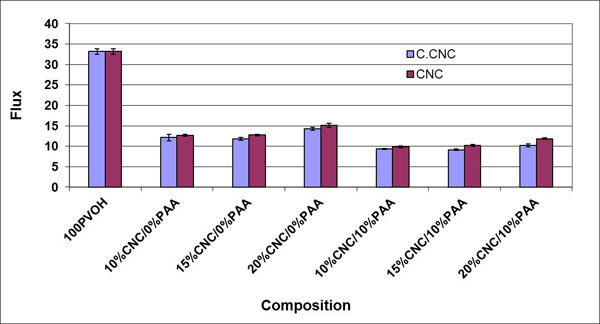
Recent and current projects have studied compatibilization of cellulose in polyethylene; cellulose/polysulfone nanocomposites; cellulose carboxymethyl cellulose nanocomposites, cellulose/polyvinylalcohol nanocomposites, and DNA/CNC hybrid nanomaterials. Additional projects targeting biomedical applications are also underway.

We are also investigating cellulose nanocrystal aerogels. These interesting systems allow us to study fundamental interactions in composites and obtain a close up view of CNCs and their chemical and physical modifications (Fig. 6).
CNCs are being utilized to make extremely well characterized polymer nanocomposites in order to test and verify the Nairn model (R. Moon, A. Martini, J.A. Nairn, J. Simonsen, and J. Youngblood, "Cellulose Nanomaterials Review: Structure, Properties and Nanocomposites," Chem. Soc. Rev., 40, 3941-3994 (2011). DOI:10.1039/C0CS00108B). The Nairn model is a set of equations that includes a size parameter and in interface parameter. This effort will utilize polymer infused CNC organogels to create a nanocomposite with a known particle distribution. This is also a way to investigate percolation of CNCs in polymer nanocomposites (PPTX).
Cellulose nanocrystals have a bright future due to the large number of potential applications:

